Unique Info About What Is The Minimum Best Torque
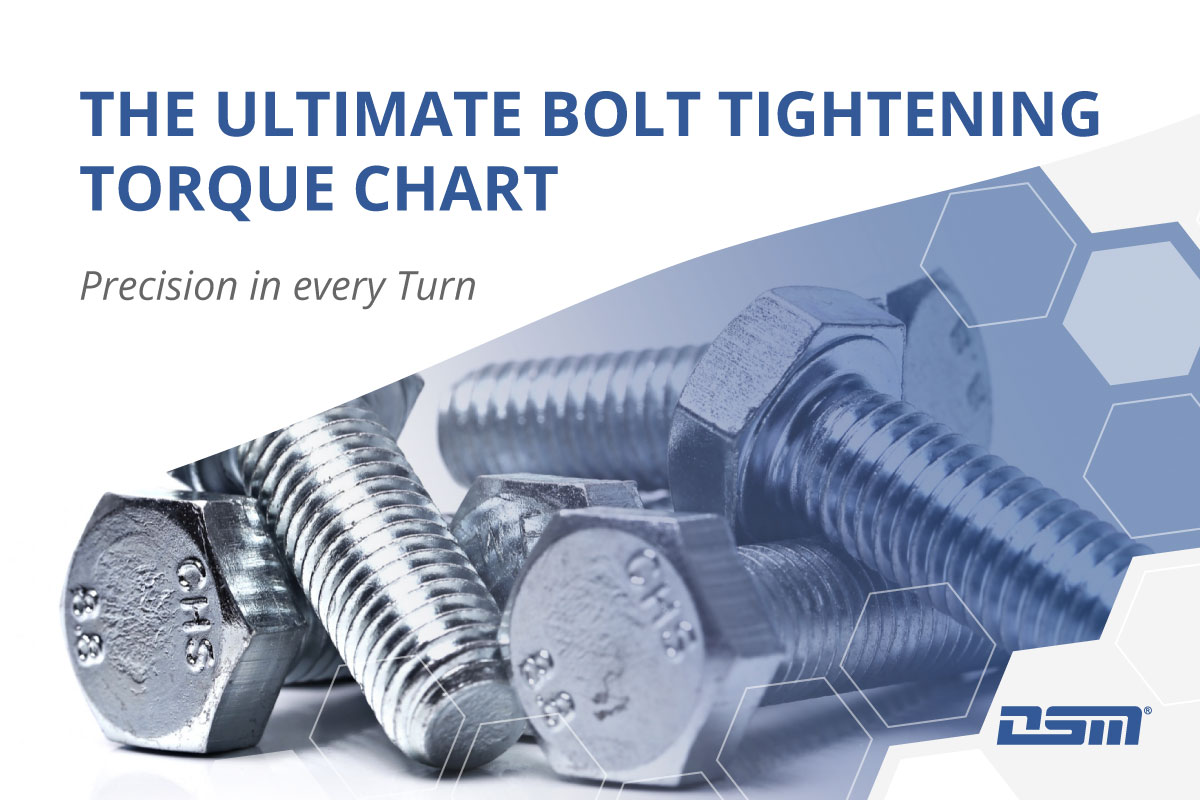
Bolt Torque Chart + Calculator For Standard Sizes
Understanding Torque
1. What Even IS Torque, Anyway?
Okay, so you've heard the word "torque" thrown around, especially if you're into cars or anything mechanical. But what does it really mean? Forget the complicated physics textbook definitions. Think of torque as the twisting force that causes rotation. It's what gets your wheels turning, your wrench tightening a bolt, or even your doorknob opening. It's the muscle behind the movement, the grunt that gets things going.
Imagine trying to loosen a really stuck bolt. If you use a tiny wrench, you might strain and strain without any luck. But if you grab a wrench with a longer handle, suddenly it's much easier! That's because the longer handle gives you more leverage, which translates to more torque. Its not just about how hard you push; its about how effectively you can turn something.
Torque is typically measured in pound-feet (lb-ft) or Newton-meters (N-m). The higher the number, the greater the twisting force. So, a car with 300 lb-ft of torque can generally accelerate faster than a car with only 200 lb-ft, all other things being equal. Think of it as the "get-up-and-go" force.
But here's the kicker: torque isn't everything! Horsepower also plays a crucial role, especially at higher speeds. Think of horsepower as how long you can sustain that twisting force. Torque gets you moving; horsepower keeps you moving at a good clip.

Delving into the Realm of Minimum Best Torque
2. Finding the Sweet Spot
Now, let's get to the heart of the matter: what's the minimum best torque? That's a bit of a tricky question because it depends entirely on the specific application. There's no one-size-fits-all answer. What's sufficient for tightening a tiny screw on your glasses is dramatically different than what's needed to climb a steep hill in a loaded pickup truck.
When we're talking about the minimum best torque, we're really aiming for the lowest amount of torque that still allows you to accomplish the task safely and effectively. In some cases, minimum means avoiding overtightening and stripping threads. In others, it means ensuring sufficient power to perform a job without damaging equipment or creating a safety hazard.
Consider tightening wheel lug nuts. Too little torque, and your wheel could come loose while driving — a terrifying thought! Too much torque, and you could warp the rotor or even snap the studs. There's a specific range, usually printed in your owner's manual, that represents the minimum best torque for that application. It's the point where you achieve adequate clamping force without risking damage.
The minimum best torque is actually a crucial concept in engineering and design. Over-engineering (using way more torque than necessary) can lead to increased costs, unnecessary weight, and even component failure. Conversely, under-engineering (not using enough torque) can lead to catastrophic failures and dangerous situations. It's about finding the Goldilocks zone: just right.

Introduces Proudly USA Built & Serviced CE / EU Safety Certification
Why "Minimum Best Torque" Matters in Real Life
3. Applications Beyond the Garage
The concept of minimum best torque isn't just confined to mechanics and gearheads. It pops up in all sorts of places you might not expect. Think about robotics, for instance. A robot arm designed to pick up delicate objects needs just enough torque to grip without crushing them. Too much torque, and splat — you've got a mess. Too little, and the object slips from its grasp.
Even in medicine, torque plays a vital role. Surgeons use specialized tools that require precise torque control. Imagine a surgeon inserting a screw during a spinal fusion procedure. They need to apply just the right amount of torque to secure the implant without damaging the surrounding tissue. Too much force, and they could injure the patient. Too little, and the implant won't be stable.
Then there's manufacturing. Assembly lines rely on automated tools that apply consistent torque to fasteners. This ensures that every product is assembled correctly and meets quality standards. From smartphones to airplanes, the minimum best torque is carefully calculated and controlled to guarantee reliability and safety.
Think about power tools. Many drills and impact drivers have torque settings. These settings allow you to adjust the amount of torque applied to the fastener. This is incredibly useful because it prevents you from stripping screws or damaging the material you're working with. By dialing in the minimum best torque, you can achieve professional results without overdoing it.
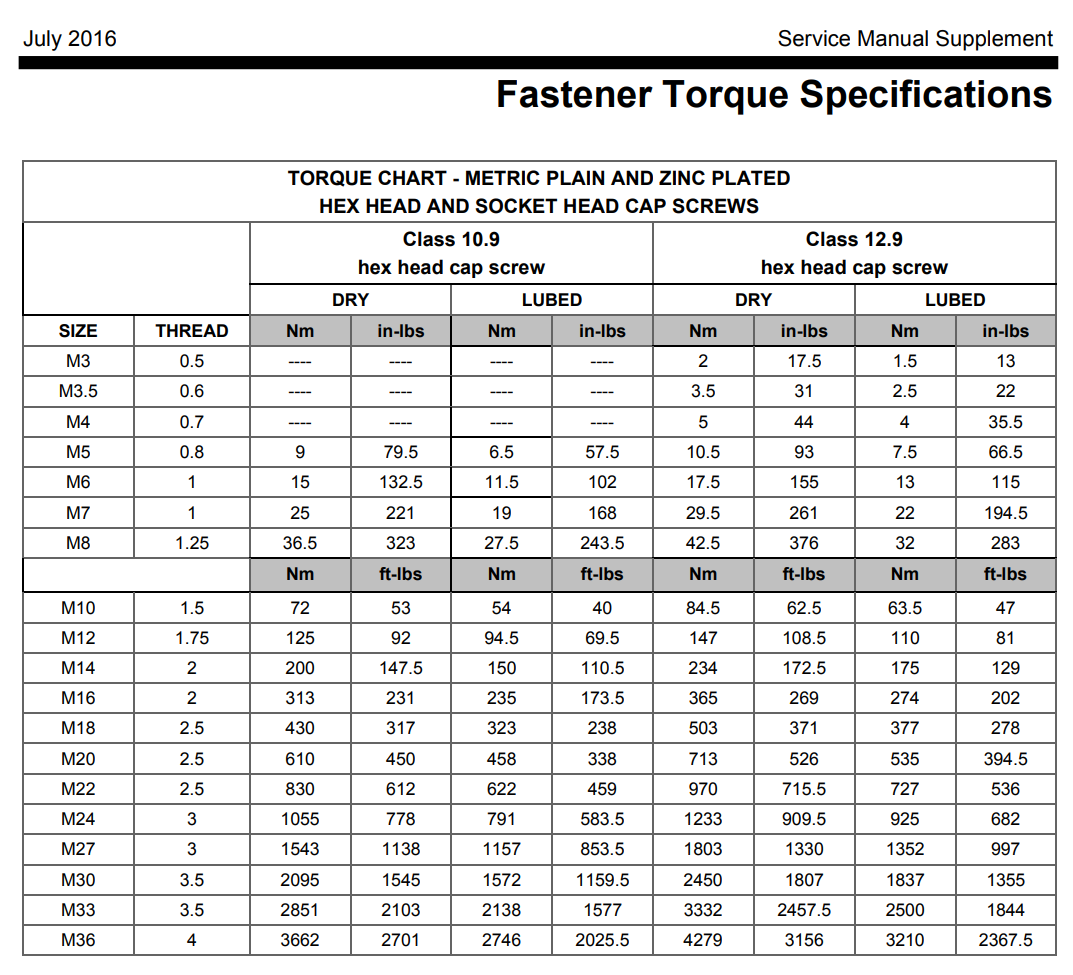
Metric Bolt Torque Settings Chart
Factors Influencing the Minimum Best Torque
4. More Than Just a Number
Determining the minimum best torque for a given application isn't as simple as pulling a number out of thin air. Several factors come into play, including the materials involved, the size and type of fastener, the operating environment, and the desired level of safety and reliability. Let's break down some of these key considerations.
First, the materials. A bolt tightened into aluminum requires significantly less torque than the same bolt tightened into steel. Aluminum is softer and more prone to stripping, so you need to be more careful. Similarly, the type of fastener matters. A fine-threaded bolt generally requires less torque than a coarse-threaded bolt because it provides more clamping force for a given amount of rotation.
The operating environment also plays a crucial role. If the joint is exposed to extreme temperatures or corrosive substances, you might need to increase the torque slightly to compensate for expansion, contraction, or material degradation. Vibration is another factor to consider. If the joint is subject to constant vibration, you might need to use locking fasteners or apply a thread-locking compound to prevent it from loosening over time.
Finally, safety and reliability are paramount. In critical applications, such as aircraft or medical devices, the minimum best torque is often determined using rigorous testing and analysis. Engineers will conduct fatigue tests, stress tests, and other experiments to ensure that the joint can withstand the expected loads and conditions without failing. This process helps to establish a safety margin and minimize the risk of accidents or malfunctions.

Best Torque Wrench In 2024 The Wrenches Our Top 5 Picks Will
Tools and Techniques for Achieving Minimum Best Torque
5. Getting It Right, Every Time
So, how do you actually achieve the minimum best torque in practice? The most common tool for this job is a torque wrench. A torque wrench is a specialized wrench that allows you to precisely measure and control the amount of torque applied to a fastener. There are different types of torque wrenches, including click-type, beam-type, and electronic models. Click-type wrenches are the most popular because they're easy to use and provide an audible "click" when the desired torque is reached.
Before using a torque wrench, it's essential to consult the manufacturer's specifications or a reliable torque chart to determine the correct torque value for the application. These charts typically list torque values for various fastener sizes, materials, and thread types. It's also important to ensure that the threads are clean and lubricated. Dirty or rusty threads can increase friction and lead to inaccurate torque readings.
When tightening a fastener with a torque wrench, apply a smooth and steady force until the wrench clicks or indicates that the desired torque has been reached. Avoid jerky or abrupt movements, as this can cause the torque to be inaccurate. If you're using a click-type wrench, make sure to stop applying force as soon as you hear the click. Continuing to apply force after the click can damage the wrench or over-tighten the fastener.
Regularly calibrate your torque wrench to ensure its accuracy. Torque wrenches can drift out of calibration over time, especially with heavy use. Calibration services are available at many tool shops and automotive supply stores. By taking the time to calibrate your torque wrench, you can ensure that you're applying the correct torque every time and avoiding costly mistakes.
